Common Construction Types for Commercial Buildings
So, you're thinking about what type of construction most commercial buildings are made of, huh? Well, you're in the right place! Commercial buildings are like the backbone of urban areas—a solid mix of creativity and practicality. Without them, we wouldn't have places like malls, office spaces, or hotels. But what really holds these structures together? The answer isn’t as straightforward as you might think.
In the world of commercial construction, steel framing, reinforced concrete, and even prefabricated buildings are the main game-changers. These methods are preferred for their strength and cost-efficiency. But here's the thing: the choice of construction type isn't just about price or materials. It also considers regional weather, building purpose, and even the aesthetic vibe a business wants to project.
Ever walked into a high-rise and marveled at the endless glass and steel? That's steel frame construction for you. Its rigid skeleton allows buildings to reach impressive heights without compromising structural integrity. On the other hand, concrete structures offer unrivaled soundproofing and fire resistance, making them perfect for places like theaters and schools.
Then there's the intriguing world of prefabricated construction. It’s not just for residential houses anymore. Prefabs are shaking up the commercial scene with their quick assembly and minimal waste, appealing to eco-friendly builders and budget-conscious developers alike.
- Steel Frame Construction
- Reinforced Concrete Structures
- Prefabricated Buildings
- Choosing the Right Method
Steel Frame Construction
When it comes to commercial construction, steel frame construction is a big player. It's valued for its ability to support tall, spacious buildings without requiring thick internal support walls. This makes it perfect for skyscrapers and large commercial complexes you'd find in city centers.
So, why steel? For starters, steel is incredibly strong and surprisingly light compared to concrete. It allows architects to design dynamic buildings with large open spaces, making interiors more flexible for whatever business needs their rooms to meet. The strength-to-weight ratio also means seismic and wind loads are managed efficiently, contributing to safety. Who wouldn't appreciate that?
Advantages of Steel Frame Construction
- Flexibility: The steel framework can adapt to various designs and changes during the building process without significant delays.
- Durability: Steel doesn't warp, crack, or grow mold, and it's less susceptible to termites and other pests, meaning your structure stands the test of time.
- Speedy Construction: Prefabricated steel components enable faster assembly, reducing construction time considerably, and time is money in the business world.
- Recyclability: Steel is one of the most recycled materials on the planet, so if sustainability is important to you, this is a huge plus.
Material | Strength (MPa) | Weight (kg/m3) |
---|---|---|
Steel | 400 - 550 | 7850 |
Concrete | 20 - 70 | 2400 |
Looking at these numbers, it's not hard to see why steel is a staple in commercial building projects. Of course, it's not always the go-to choice for every project. Factors like cost, design, and building location may sway decisions. Nevertheless, for those planning a sturdy, modern high-rise or sprawling commercial center, steel frame construction is definitely worth considering.
Reinforced Concrete Structures
Let's talk about reinforced concrete – the superstar of commercial construction. This stuff is everywhere; from skyscrapers to stadiums, it's kind of the unsung hero holding up the modern world. But what makes it so great?
First off, reinforced concrete combines concrete with steel bars, which people call rebar, to boost its strength. Concrete alone is pretty fantastic at handling weight, but when it comes to bending or stretching, not so much. That's where the rebar works its magic, providing tensile strength to the mix. It's like peanut butter and jelly – better together!
Benefits of Using Reinforced Concrete
This material is more than just tough; it’s durable and low maintenance, too. If we look at buildings that have stood for decades, reinforced concrete often gets the credit. Plus, it's fire-resistant, which is a huge plus for any business worried about safety.
One of the coolest things is how customizable it is. You can mold it into virtually any shape, making it possible to design stunning architectural masterpieces. Think of the Sydney Opera House or even highway overpasses that twist and turn effortlessly through landscapes.
Advantages | Description |
---|---|
Strength | Combines the compressive strength of concrete with the tensile strength of steel. |
Durability | Resistant to weathering and exposure to harsh elements. |
Fire Resistance | Can withstand high temperatures without losing integrity. |
Challenges with Reinforced Concrete
But wait, it's not all sunshine and rainbows. One downside is it can be pretty heavy, requiring a solid foundation, and it can take some time to cure properly before it's at full strength. There's also a thing called "concrete cancer," which sounds scary but refers to the deterioration of the reinforced steel bars due to corrosion—and yeah, it’s a real issue if not dealt with early on.
In the end, choosing reinforced concrete for a commercial building is like picking a trusty workhorse. It might not be flashy, but it'll get the job done right—and for a long time.
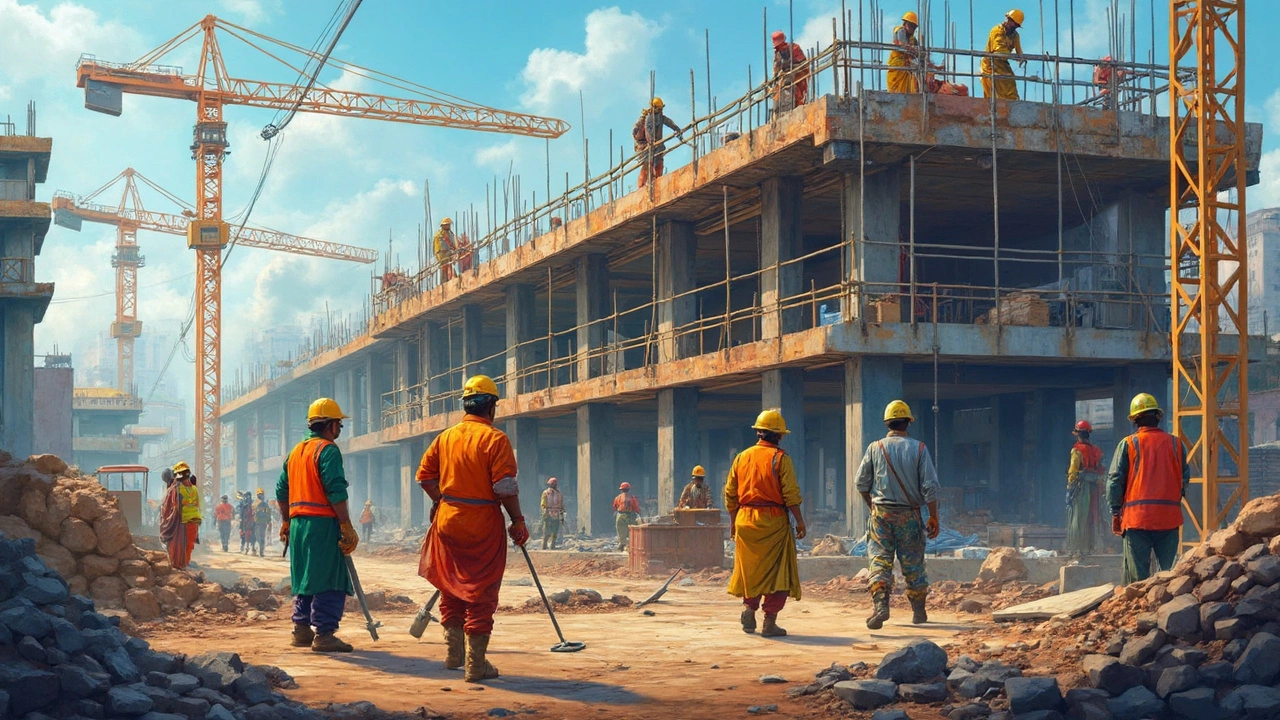
Prefabricated Buildings
Prefabricated buildings are like the secret weapon of the commercial construction world. They're all about assembling things off-site in a factory and then shipping them to the build location for quick assembly. Talk about efficiency! This method not only cuts down on waste but also speeds up the construction process like you wouldn't believe.
Now, why are prefabricated buildings such a hit in the commercial sector? First off, they save a ton of time. Imagine having most of the construction work done away from the site, which means there's less weather disruption. Rain or shine, prefabs keep rolling. Plus, they’re super flexible with design. You can still customize the look and feel without losing out on the benefit of being cost-effective.
Benefits of Prefabrication
- Quick Turnaround Time: Projects that might take months can often be cut down to weeks.
- Eco-Friendly: Less waste and often, more sustainable materials are used in prefabrication.
- Cost-Effective: Less labor, fewer delays, and reduced material waste all contribute to cost savings.
Prefabrication isn’t without its challenges, though. While the construction part is simpler, solid planning is crucial. Any mistake in the planning stages can lead to hiccups during assembly, which can be expensive to fix.
Real-World Impact
So how's this playing out in the real world? Take a look around, and you'll see everything from schools and hospitals to trendy office buildings being constructed with prefabs. In cities trying to expand quickly and sustainably, prefabricated construction is welcomed with open arms.
As of 2023, around 10% of new commercial constructions in developed urban areas use some form of prefabrication. And it's a number that’s climbing as technology and design methods improve.
Considerations Before Choosing Prefabrication
- Planning: Requires meticulous planning and upfront design decisions.
- Logistics: Transportation and assembly need thorough coordination.
So, if you're on the hunt for a building method that’s both green and efficient, prefabricated buildings might just be your answer. Just make sure you've got a rock-solid plan before you dive in!
Choosing the Right Method
Picking the right construction method for a commercial building isn't just about pulling numbers out of a hat or going with personal gut feeling. It's a process that involves understanding different needs and making strategic decisions. Let's break it down.
Consider the Building's Purpose
The purpose of the commercial building often dictates the construction type. For instance, office spaces thrive with a steel frame construction because it's sturdy and flexible enough to accommodate changes in layout or additional floors down the line. On the other hand, entertainment venues might prefer reinforced concrete for its acoustic properties.
Location, Location, Location
Where your building is situated plays a huge role. In coastal areas, for instance, steel might be galvanized to prevent corrosion due to salty air. Meanwhile, regions prone to earthquakes might lean towards reinforced concrete because of its superior shock absorption.
Budget and Timeline
Budget constraints and time are often the deciders in the world of commercial construction. Prefab buildings are gaining popularity precisely because they're cost-effective and quick to erect. This method cuts down construction time by about 50% compared to traditional techniques, saving money on labor costs too.
Environmental Impact
Today's builders have a growing responsibility to minimize their surroundings' environmental impact. Prefabricated buildings tick many eco-friendly boxes due to reduced waste, and using recyclable materials. Meanwhile, steel and concrete can be sourced sustainably, but it requires some homework to get suppliers who meet these criteria.
Factor | Ideal Construction Method |
---|---|
High Altitude | Steel Frame Construction |
Quick Turnaround | Prefabricated Buildings |
Acoustic Needs | Reinforced Concrete |
Ultimately, weighing these factors carefully can lead to the best choice for your project. It’s all about balancing your needs with what's feasible, both logistically and financially.
Comments