Civil Construction: What It Includes and Why It Matters for Commercial Projects
Ever stood in front of a fancy new office building and thought about what’s going on underneath? Before a building goes up, there’s a lot happening in the dirt below—civil construction is where the action starts. If you’re thinking of launching a commercial project, it helps to know exactly what civil construction teams do. You’re not just hiring diggers and concrete pourers. You’re kicking off a massive process that’s all about making the land safe, stable, and ready for business.
Civil construction covers all the behind-the-scenes work—think moving earth, installing big pipes for water and drainage, flattening roads, and pouring the first layers of concrete or laying down steel. If you’ve ever swapped stories with someone who’s built a retail complex or a warehouse, you know the unexpected stuff comes up below the ground: buried junk, soggy soil, old pipes in the way. There’s a right way to do it, and it saves big headaches (and money) later on. Every choice you make in this phase shapes the future of the build. Want your project to last? Get this part right from the start.
- Breaking Down Civil Construction
- Starting from the Ground Up: Earthwork and Site Prep
- Underground Utilities: The Heartbeat of Any Site
- Concrete, Steel, and Paving: Shaping What You See
- Key Players and Project Management Tips
- What to Watch for: Common Hurdles and Smart Solutions
Breaking Down Civil Construction
If you’re picturing bulldozers and cement trucks, you’re on the right track, but civil construction stretches way beyond that. In commercial construction, civil work sets the whole tone for a project. It’s all about taking a raw piece of land and shaping it into something that can safely support everything to follow. You can’t skip this stuff or cut corners—investors, owners, and insurance folks care about it for a reason.
So, what actually falls under the civil construction category? It covers all the major groundwork and site-related tasks:
- Clearing and grading land
- Earthmoving for foundations and roads
- Setting up stormwater drains and big sewer lines
- Pouring concrete slabs, curbs, and gutters
- Installing all underground utilities (think water, power, comms)
- Building retaining walls and shoring up slopes
- Laying asphalt for access roads and parking lots
According to the Civil Engineering Research Foundation,
"Nearly 60% of project delays in commercial construction start in the civil phase, mostly because unexpected site conditions get overlooked."That’s a wild number, and it shows how important planning and investigation are in this part of the job. Getting the dirt right makes everything else run smoother and, honestly, can shave months off your build time.
Here are a few fast facts every owner or contractor should know:
Task | Typical Share of Construction Budget (%) |
---|---|
Earthwork & Grading | 15-20 |
Underground Utilities | 7-12 |
Concrete & Paving | 10-18 |
Don’t let anyone tell you civil work is just the “messy” phase. It’s where you decide if your parking lot floods each spring, or if your site drains properly forever.
The bottom line? Civil construction is the foundation (literally and figuratively) of every successful commercial building. Get it wrong, and you pay for it twice.
Starting from the Ground Up: Earthwork and Site Prep
Earthwork is where civil construction really gets rolling. Before a single wall goes up, teams tackle the land itself. This part is all about moving dirt—sometimes tons of it—and shaping the ground to fit the plans. In commercial projects, the goal is to make sure the site is stable and ready for everything else that’ll be built on top.
There are a few main steps every solid earthwork job follows:
- Clearing: First, crews clear trees, rocks, old asphalt, or anything else blocking the way. No point pouring concrete on last year’s forgotten driveway.
- Grading: This step means leveling the site, creating slopes where water can drain safely away from the buildings. Get this wrong, and you’ll have puddles under your future lobby.
- Excavation: Digging down for foundations, basements, or underground utilities is key. Some projects go just a few feet, others need holes big enough for heavy machinery or multi-level parking structures.
- Soil Testing: After digging, geotechnical teams test the soil to check it’s solid enough for heavy loads. Bad soil? Out comes the compactor, or sometimes crews dig deeper and haul in better fill material.
- Compaction: At every stage, the dirt is packed down tight, so it won’t shift once construction starts. The strength of your foundation? It’s only as good as the compacted dirt underneath.
Here’s a quick look at how much earthwork can add up on a commercial job:
Site Size (acres) | Average Cubic Yards Moved | Typical Duration (weeks) |
---|---|---|
1 | 3,000 – 4,500 | 2 – 4 |
5 | 12,000 – 20,000 | 4 – 8 |
20+ | 50,000+ | 8 – 16 |
One overlooked tip? Always check for hidden surprises. It’s not rare to find old fuel tanks, buried cables, or even forgotten sewer lines once digging starts. I remember a big box store build where the site crew found a slab foundation from a 1950s warehouse. Fixing that delayed the project by a week. Having good site surveys up front isn’t just paperwork—it actually saves time, money, and headaches.
Underground Utilities: The Heartbeat of Any Site
Picture this: without water lines, power cables, or a proper sewer system, your new building is basically just a big, fancy shed. Laying civil construction groundwork isn’t just about dirt and concrete—it’s about putting in the systems that keep everything running smoothly inside and outside those walls. Underground utilities might not sound exciting, but skip them or mess them up, and you’re in for big trouble later. City inspectors are not known for forgiving mistakes here.
So, what do we mean by "underground utilities"? You’re looking at all the main lifelines: water mains, fire protection, stormwater pipes, sewer lines, and power or communication conduits. Gas lines, too, if you’re cooking or heating with gas in your space. Each one has strict rules about placement, depth, and materials. If someone’s coming to dig, you’d better know where these are—one wrong move can mean busted water mains or blackouts in half the block.
- Water supply: The pipes usually run deeper in cold climates to prevent freezing and must have backflow preventers to stop contaminated water flowing into clean lines.
- Sewer and drainage: These work by gravity, so they need careful slope calculation. Mess that up, and you’ve got blockages and backups—never fun to explain to an angry client.
- Power and communication: Fiber optic cables, copper lines, and heavy-duty electrical conduits get separated into their own trenches or ducts for safety.
- Gas lines: Marked by color (yellow for gas), they follow strict safety codes and distances from other lines.
If you’re wondering about the costs (who isn’t?), take a look at this real breakdown for a typical commercial build in the U.S.:
Utility Type | Typical Cost per Linear Foot (2024 Data) |
---|---|
Water Main Installation | $50 - $150 |
Sewer Line Installation | $60 - $200 |
Stormwater Drainage | $40 - $120 |
Power / Communications | $20 - $90 |
Natural Gas Line | $30 - $75 |
If you’re in a city, you’ll also deal with permit fees, inspections, and sometimes surprises like old, abandoned lines or contaminated soil. Plans can change in a hurry—always budget extra time and money for the unknowns.
Tip from experience: Always use utility locating services before digging. There’s literally a national “Call Before You Dig” hotline (call 811 in the U.S.) that can save a fortune and keep everyone safe. And if you want your building handed over to you on schedule, sweating the underground details is the real secret sauce.
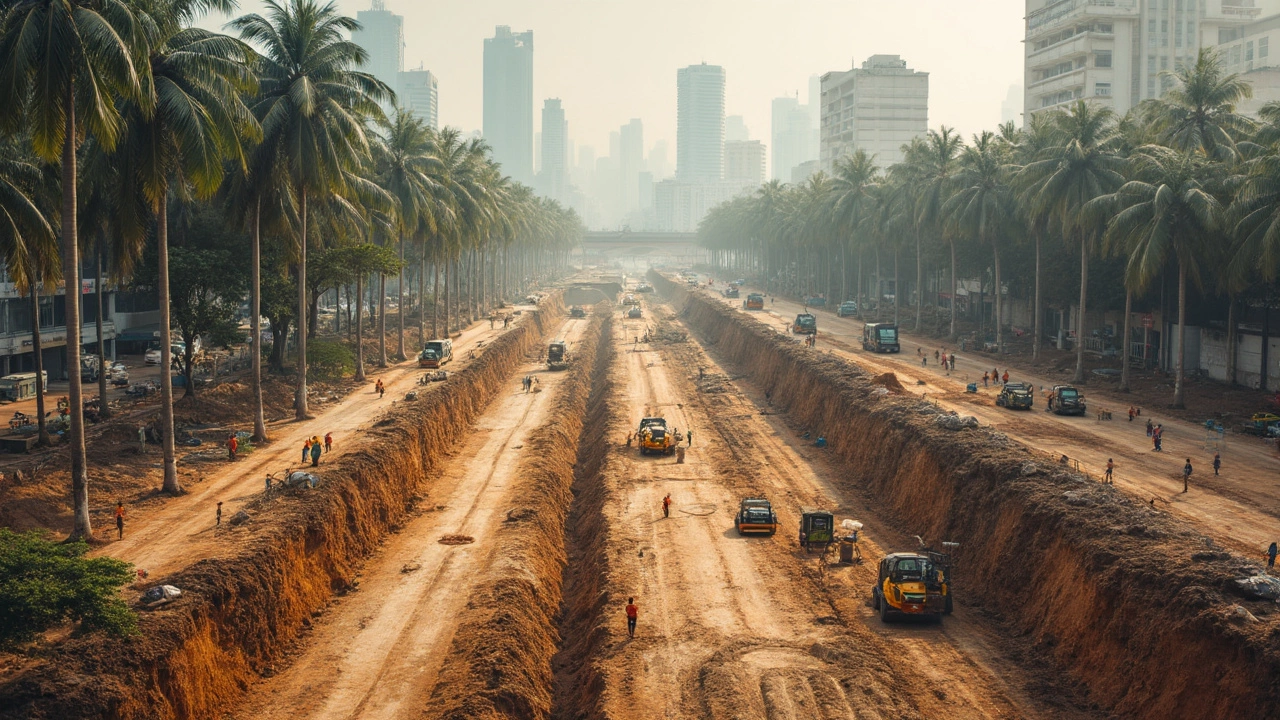
Concrete, Steel, and Paving: Shaping What You See
This is where a commercial site starts looking less like a construction zone and more like something you recognize. You’ve got heavy machines rolling in, crews in reflective vests, and suddenly there’s a slab where there was just mud. Every office block, shopping center, or warehouse relies on a smart mix of concrete, steel, and blacktop—and getting this right makes the difference between a rock-solid build and a never-ending snag list.
Most folks don’t realize that about 40% of all concrete poured in the U.S. each year goes to civil construction projects like commercial buildings and their support structures. Why? It holds up everything from your front lobby to parking structures. Steel is close behind, used for framing, supports, reinforcing bars (rebar), and bridges onsite. You want these materials to meet the right specs: design, thickness, even weather resistance, or your project could end up with sagging floors or cracks before anyone moves in.
- Concrete: It’s not just about pouring and praying. Commercial projects need different concrete mixes for foundations, slabs, sidewalks, and loading docks. High-strength mixes are standard for floors that’ll see forklifts or heavy equipment.
- Steel: It gets welded, bolted, and tied into just about every big structure. Local codes control what kinds and grades you can use—for example, wider beams in an otherwise tight warehouse layout.
- Paving: Asphalt and concrete paving cover roads, parking lots, and driveways. Thickness matters; skimping by even an inch can cost thousands in repairs later. Don’t cheap out on sealant, either—it keeps water from sneaking in and wrecking everything below.
If you’re setting a project schedule, expect delays if weather hits during concrete pours. Cold snaps or rain can mess with curing, and steel needs dry days to avoid rust and safety hazards. Here’s a look at how much material it takes for just a mid-sized 100,000 sqft commercial site:
Material | Approximate Quantity | Comments |
---|---|---|
Concrete | 3,000-5,000 cubic yards | Depends on design; includes parking areas |
Steel | 200-300 tons | Framing, rebar, beams |
Asphalt | 6,000-8,000 tons | Parking lots and roads |
Want a tip? Always check if the contractor is using certified materials and following the approved specs. Cutting corners here leads to repairs down the line. Also, a lot of cities now offer incentives if you use recycled materials, like crushed concrete and steel, so you’ll save cash and help the planet at the same time.
Key Players and Project Management Tips
If you want your civil construction job on a commercial site to run smooth, you need the right crew and some solid planning. There are a few teams and people you really can’t do without. Let’s break down who typically runs the show and how you can keep everything organized—even when the job gets messy.
The civil construction team usually includes:
- Project Manager: Calls the shots, keeps everyone on task, solves problems as they pop up.
- Civil Engineers: Designs the plans, checks safety, and signs off on big decisions.
- Site Supervisors: Keeps the day-to-day work humming, deals with subcontractors and suppliers directly.
- Foremen: Manages crews on the ground, keeps the work moving.
- Specialist Subcontractors: Covers things like earthmoving, concrete, or underground utilities.
Organization is half the battle. Commercial builds are notorious for tight timelines and strict budgets. According to the Construction Industry Institute, just 31% of large projects actually finish on time and on budget. If you want to land in that winning third, try these practical tips:
- Weekly check-ins: Stay on top of changes by huddling up once a week. These don’t have to be long—just focused.
- Clear paperwork: Get your contracts and change orders in writing, always. Lost paperwork costs time and money.
- Track equipment and materials: Use a simple spreadsheet or even a construction app. Stolen or missing gear is a real headache—around $1 billion is lost each year to equipment theft in the U.S. alone.
- Risk planning: List the top three things that could blow up your schedule (weather, permits, surprise soil problems) and have a backup plan.
Role | Main Job |
---|---|
Project Manager | Handles overall project and solves problems |
Civil Engineer | Designs, checks safety, approves key moves |
Site Supervisor | Manages crews and site work |
Foreman | Directs ground teams |
Subcontractor | Handles specialized tasks |
If I’ve learned anything from shadowing folks like these, it’s that trust and clear talk count for more than fancy tech. Get your team talking, keep your paperwork tight, and don’t be shy to walk the site. Civil construction is complex, but if you’ve got the right people in place and a plan that flexes with reality, you’re miles ahead of most.
What to Watch for: Common Hurdles and Smart Solutions
If you’re neck-deep in civil construction, you quickly learn the old saying is true: what can go wrong, will go wrong—unless you plan for it. For commercial sites, the surprises are rarely minor. Think mud that won’t quit, utilities not mapped on any city record, or steel that shows up late. Let’s look at the most common speed bumps and some ways the pros handle them.
- Unstable Soil and Groundwater Issues: A lot of sites have soil that’s not as tough as you’d hope. Too sandy, too wet, or full of clay—any of these can tank your timeline if you don’t catch them early. Get a good geotechnical survey. In the U.S., over 80% of commercial projects now start with one. If you’re dealing with groundwater, well-placed sump pumps or soil stabilization can save the day.
- Hidden Utilities and Oops Moments: Nobody likes digging into a surprise gas line. Always use up-to-date scanning equipment before breaking ground. In a 2023 survey, utility strikes cost U.S. construction crews nearly $1.7 billion. Call 811 or the local equivalent. Don’t risk it.
- Scheduling Crunches and Delivery Delays: Materials are only as good as their arrival time, and delays happen. Track delivery status obsessively and keep a local backup supplier on speed dial. If steel or concrete is late, reshuffle tasks so crews stay busy and time isn’t wasted.
- Permits, Inspections, and Red Tape: Permit delays are notorious in commercial builds. Assign someone on your team whose sole job is to chase down and follow up on permits and inspections. Having a single point of contact keeps things moving and avoids crossed wires.
- Safety, Safety, Safety: Accidents shut down jobs and raise insurance costs. On big sites, weekly toolbox talks and real-time safety apps (like SafetyCulture or iAuditor) have been a game changer for keeping teams on track.
Here’s a look at what typical civil construction hurdles cost in both time and money:
Common Issue | Average Delay (days) | Average Extra Cost (USD) |
---|---|---|
Unstable soil | 7-21 | $20,000+ |
Utility strike | 3-10 | $15,000-$50,000 |
Permit delay | 5-30 | $5,000-$25,000 |
Equipment breakdown | 1-7 | $2,500-$10,000 |
The smart move? Never assume the site is straightforward, and always have a plan B. Extra planning upfront avoids expensive "fix-it-on-the-fly" drama later. Commercial projects are all about juggling moving targets, but with solid checks, backup plans, and a sharp eye for the details, you’ll get through the messy bits a lot smoother.
Comments