Cheapest Building Methods: Affordable Construction Techniques Explained
Ever looked at a basic shed or a humble cabin and thought, "How'd they build that for so little?" The cost of construction—whether it’s a tiny house, a modest family home, or even a commercial space—can vary wildly. But if you peel back the layers, the secret sauce comes down to the building methods and materials people choose. In the UK, the search for affordable housing is almost a sport on its own. Even in my own backyard here in Manchester, there’s plenty of buzz about creating something solid without torching your savings. But what’s the real trick to the cheapest building method? This isn’t about cutting corners or going cheap-and-nasty. It’s about smart design, innovative materials, and sometimes, a little bit of doing it yourself (with your cat staring judgmentally). Pull up a chair—let’s get into what drives building costs down, what the cheapest techniques are, and what actually works when you want affordable but don’t want to eternally patch leaky roofs or shiver in winter.
What Drives Costs in Construction? The Big Picture
Before you can chase down the cheapest building method, you’ve got to know what steamrolls your budget in the first place. It’s rarely just one thing—more like a herd of wallet-thirsty issues. Land prices, local planning fees, energy bills, materials, skilled trades, machinery hire—they all add up. Let’s not forget the unexpected "small" things: insulation, fittings, or sudden planning surprises. In the UK, recent ONS data showed average construction material prices spiked nearly 24% between 2021 and 2024. Timber, for example, which was once as affordable as a night at the pub, tripled in price during COVID then settled down—just a bit. Cement, steel, and insulation materials haven’t exactly dropped in price, either.
There’s also labor to factor in. Skilled builders cost real money, and the shortage of skilled tradespeople drives costs higher, especially for specialized jobs like stone masonry or heritage brickwork. Architect fees? They can range anywhere from £2,000 for a simple small home plan to over £20,000 for custom, detailed designs—with the average commission sitting at 7% of the build price. Now, if you DIY a chunk of the work, you save on labor, but not everyone fancies risking life and limb on a ladder (or braving the wrath of UK weather). Regulatory requirements—think insulation, fire resistance, planning consents—aren’t negotiable, but innovative methods such as modular or prefab construction can help skirt some of the most time-hungry, expensive steps.
Hidden costs crop up, too: delivery fees, waste disposal, tool hire, and sometimes-thieving neighbours (don’t ask me about my missing wheelbarrow—Whiskers didn’t see a thing). Location also matters. Building in rural Scotland isn’t like building in central Manchester. Transporting materials and labour to out-of-the-way places can cost more than the materials themselves. It’s no joke—according to a 2024 RICS survey, remote builds can be 15-35% pricier just for logistics.
Item | Average Cost Increase (UK, 2024) |
---|---|
Timber | +17% |
Concrete | +12% |
Insulation | +9% |
Labour | +8-13% |
Transport (remote) | +20-35% |
So, what do you do? You can’t control land prices (unless you inherit it), but you can get clever with methods, design, and what goes into your build.
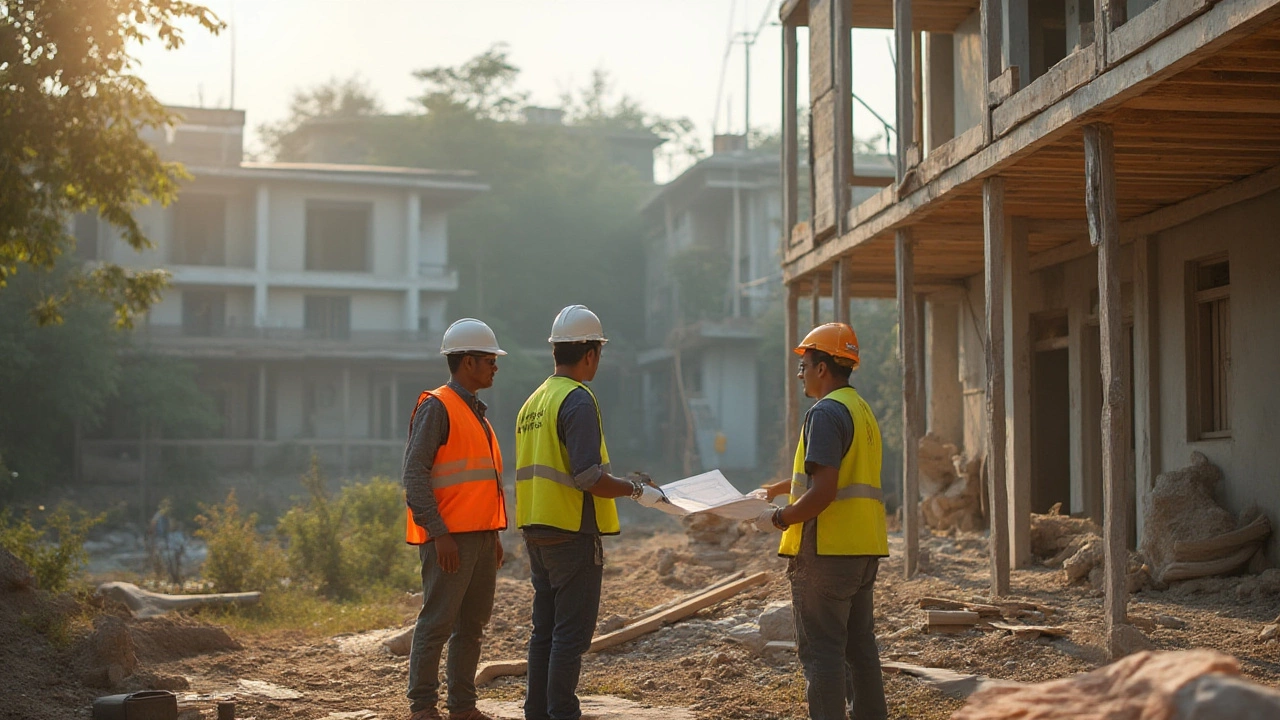
Cheapest Building Methods From Bricks to Bales: Real-World Choices
Right, so let’s dive into the material world. If saving money is your top priority, brick-and-block isn’t usually your cheapest bet, even though it’s still the standard for much of the UK housing stock. A basic brick house can run £1,200–£1,800 per square metre—higher for anything fancy. So, what are your options?
- Timber Frame Construction: Quick to build and often lower labour costs. Timber frames can range from £900 to £1,400 per m2 in 2025. But you need good insulation in the UK climate, and timber must be well-treated to resist damp and pests. Still, it’s the darling of eco-builders and self-builders trying to keep budgets lean without sacrificing quality.
- Structural Insulated Panels (SIPs): Massive in the USA, gaining traction here. Quick to erect, great energy efficiency, fewer on-site delays. Costs about the same as timber frame but saves big on heating over time. Includes insulation by default—smart.
- Modular & Prefabricated Units: Built off-site, delivered and assembled like Lego. They shrink build time, trim labour costs, and reduce waste. Some modular homes start as low as £50,000 for shell-and-core, with completed homes hitting £1,000–£1,250 per m2. Plus, you can guarantee a weatherproof structure in days, not weeks, reducing the typical UK "soggy wood" problem.
- Shipping Containers: Sounds wild, but lots of folks now turn old containers into homes or offices. They’re tough as nails and can be joined for extra space. A basic 40ft unit can run as little as £2,200 (bare) up to £25,000 (fully converted, insulated, plumbed). Downsides? Insulation is crucial, and they need good ventilation, but for funky, ultra-cheap builds, they’re hard to beat.
- Earthships and Rammed Earth: Forget traditional walls—use soil from your actual plot, mixed with a bit of cement or lime. Rammed earth walls can be absurdly cheap if you DIY (materials in the hundreds), though labor can drive costs up fast if you hire out. Earthships go further, using tires, bottle walls, and more. It’s green, budget-friendly, and suits temperate climates if you get the details right. Only catch: they take time and sweat equity.
- Straw Bale and Cob: Picture stuffing straw into wall frames. Seriously! Straw bales (from local farmers) are cheap, super-insulating, and quick to stack. Render them with lime and they’ll last decades. A 3-bedroom straw bale home in Wales was built for under £80k in 2023, mainly by friends and volunteers—£500/m2 all-in. Cob (mud mixed with straw and clay) also costs peanuts compared to bricks but demands hard work.
Crazy as some of these sound, they’re legit. Cambridge University’s 2022 report on alternative UK homes found straw bale and timber frame buildings had, on average, the lowest lifetime costs and best sustainability scores. Prefab and modular construction is taking off, too. Urban Splash’s modular homes in Manchester, for instance, delivered modern design at nearly half the traditional cost per unit, thanks to factory efficiency and reduced waste.
Still, methods aren’t one-size-fits-all. Your cheapest route depends on local land, weather, skills available, and even local authorities (some aren’t keen on shipping containers in nice leafy suburbs). You want to check with building control or your council before going wild with any technique—no one fancies a half-built Hobbit house getting bulldozed. Speaking of regulations: UK Building Regulations insist on fire safety, energy performance, and structural strength, so don’t skimp on essentials just to save cash upfront. Cut corners, and you’ll pay later—either to fix dodgy wiring, bad damp, or emergency heating bills.
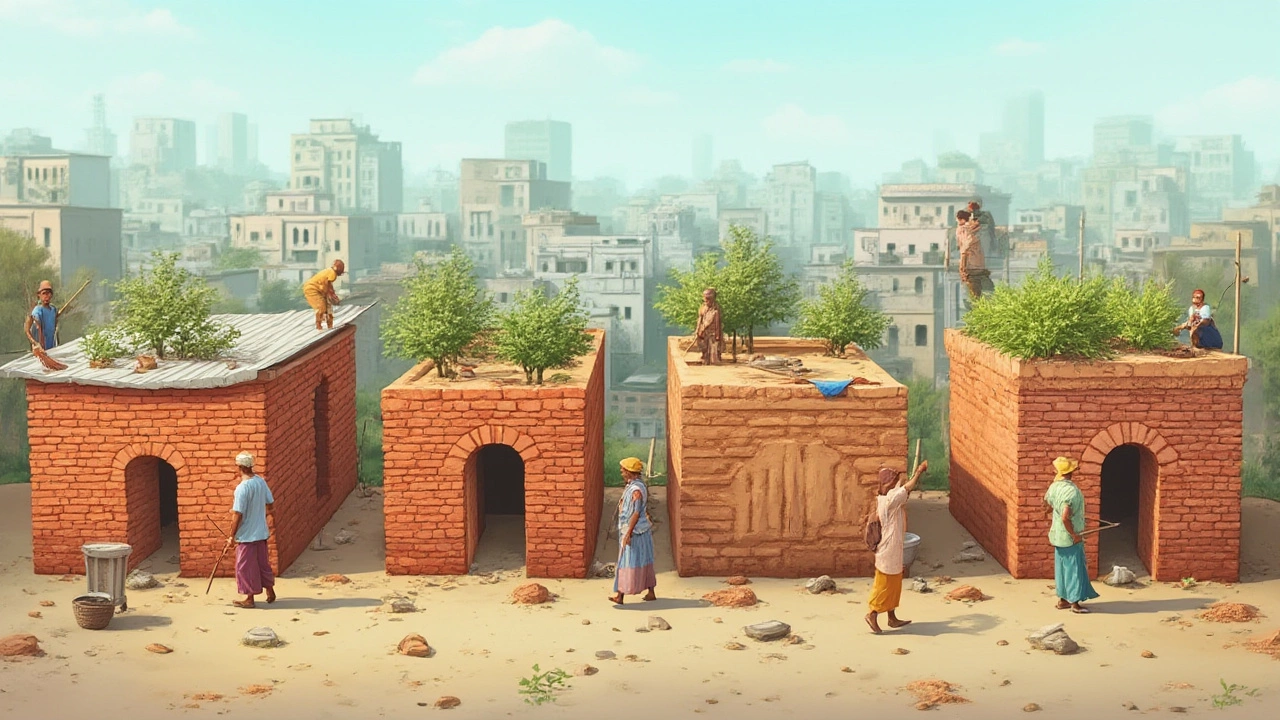
Tips and Pitfalls: How to Build Cheap and Smart Without Regrets
So, what separates a budget build that’s still solid from a money pit wrapped in tarpaulin? Here’s where penny-pinching meets real savvy. Start with design—simple shapes (think rectangles, single-storey) are easier and cheaper to build. Avoid fancy curves, split levels, or ultra-large windows. Every angle and oddity costs more in labour and materials. Go for standard door and window sizes; any custom work jacks the price. Dual-purpose spaces cut size (and cost). Need a spare room? Use a home office as a guest bedroom instead of making another extension.
Get hands-on if you can. Labour eats up to half your build budget, so some "sweat equity" goes a long way. Maybe you’re not a plastering expert, but you can paint, lay flooring, landscape, or even run cables under careful guidance. Even newcomers can manage demolition, basic framing, or insulation with some YouTube research and patience. But leave specialist tasks—structural, wiring, plumbing, gas—strictly to the pros. A bodged boiler or sketchy wiring isn’t just illegal, it’s dangerous. Trust me: mistakes can cost more to fix than doing things right the first time.
Salvage and upcycle are not just buzzwords—they’re goldmines for the wallet. Reclaimed bricks, timber, tiles, and even window frames often come at a third of new prices, look way cooler, and keep waste out of landfill. I know self-builders in the northwest who got century-old wood joists free from local demolition yards—just had to pick them up. Check auction sites and local buy/sell groups. Keep a close eye on tool hire—buying second-hand sometimes beats long-term rental.
Go local for materials where possible—cheaper transport, better match for local conditions, and fewer delays. The Brits love a good queue, but supply chain disruptions since Brexit and COVID have made local sourcing a life-saver. Bulk discounts add up, so if you’re buying insulation, plasterboard, or bricks, get quotes for multiple suppliers and negotiate hard, especially if you’re buying for more than one project or as a group. Timing your build off-peak—or at times when big projects aren’t gobbling every available tradesperson—can snag you lower labour rates.
Minimize waste. Offcuts, over-ordering, and careless storage eat profits. Fact: a 2023 study found about 10% of scheme budgets are lost to poor site waste management. Plan your cuts, maybe sell or trade leftovers, and cover unused materials from the British summer weeds and leaks.
Budget a cushion for the unknown—delays, surprise repairs, or rule changes. Even the best-planned builds get derailed by the odd storm, an angry neighbour hell-bent on blocking your daylight, or the council moving the goalposts. If you save money upfront, plan to spend a bit more on insulation, roofing, and waterproofing. No one remembers a slightly duller kitchen if the place is dry and warm through February.
Finally, don’t forget about life after the build. Cheap homes bleed cash if they’re drafty, damp, or energy-hungry. Invest upfront in insulation, draft-proofing, and solid windows—even if it means a smaller house. You'll thank yourself when the energy bills drop, and Whiskers won’t camp out on the radiator all winter.
So, what’s the answer to the cheapest building method? It's picking smart, proven alternatives—timber frame, modular, straw bale, or container—geared to your site, skills, and patience. Skip the frills, solve real issues, keep an eye on local costs, call in help for the trickier jobs, and bargain like your wallet’s life depends on it. Now, if only there were a way to stop neighbours from borrowing that last shovel...
Comments