Raw Materials for Construction: Essential Building Blocks You Need to Know
Beneath every skyscraper, beneath every cozy home, lies an unexpected world of invisible powerhouses—raw materials. Whether you’re eyeing a sleek new condo or watching a bridge rise from nothing, raw materials decide if the structure will survive a hurricane or just another rainy day. Here’s something crazy: approximately 50% of all the materials we extract globally each year are sucked up by the construction industry. That’s nearly 36 billion tons—yep, billion—with concrete, sand, steel, and wood taking the starring roles.
The Major Raw Materials Used in Construction
Let’s cut straight to the meat: what are the basic ingredients that every builder craves like a chef eyeing salt and pepper? Raw materials for construction can usually be boiled down to a shortlist—yet each comes with endless variations and flavors.
Concrete: It’s the world’s most used man-made material. At its core, concrete is just a blend of cement (think limestone cooked at wild temperatures), sand, gravel, and water. But the magic happens in the mix—whether you’re making a kitchen slab or the floor of a shopping mall, small blend tweaks can mean the difference between a surface that crumbles under kids playing tag or holds firm under trucks loaded with bricks. Fun fact: over 4 billion tons of cement are used every year, and it covers more land than all the world’s forests combined.
Steel: Want strength with a little flexibility? Enter steel. Iron ore is melted down and mixed with carbon to create steel—sometimes with other elements thrown in for resistance to rust, or extra hardness. Skyscrapers would still be a pipe dream without steel beams and rebar. If you stacked up all the steel used just in one year, it’d tower higher than Mount Everest—about two billion tons globally.
Wood: It’s ancient, renewable, and shockingly versatile. From pine framing to oak floors, the right kind of wood can make a house breathe (literally—wood absorbs moisture and releases it), or withstand brutal winters. However, the type of wood—hardwood or softwood—matters a lot. We’re burning through about 3.5 billion cubic meters of wood each year in construction alone.
Bricks and Blocks: Think small, but powerful. Made usually from kiln-fired clay or concrete, bricks are earthquake-resistant and fantastic insulators. The twist? Modern ‘blocks’ are often bigger, lighter, and engineered for quick assembly, saving time and labor costs.
Stone: Nature’s original building material. We still use granite for countertops, limestone for facades, and slate for roofs. Each kind of stone brings its superpower—granite’s toughness, limestone’s workability, or slate’s water resistance. Major public buildings often choose locally quarried stone to lower costs and carbon footprint.
Glass: You’d be shocked how much glass goes into a single office block. Glass is mostly sand (silica), baked with soda ash and lime, then often treated for specific strengths or tints. Modern glass isn’t just a window—it can hold in heat, keep out harmful sun rays, or even generate electricity with embedded solar tech.
Plastics: Not all building ‘blocks’ are hard. Plastics (like PVC) are big in pipes, window frames, and insulation. They’re light, cheap, resist rot and corrosion, and often the unsung heroes inside walls and under floors.
Asphalt: Roads, parking lots, and even flat roofs need a flexible, rain-resistant touch—cue asphalt, made from petroleum byproducts mixed with aggregate (crushed stone or sand). The best roads use a specific blend of raw asphalt for extra longevity, especially in freeze-thaw climates.
Gypsum: Drywall panels? Thank gypsum, a soft mineral that transforms into crisp, flat wallboard after a baking process. It’s lightweight, fire-resistant, and if you tap just about any wall right now, you’ll feel it hiding under the paint.
Material | Typical Use | Average Global Annual Consumption (Metric Tons) |
---|---|---|
Concrete | Foundations, walls, floors | 36,000,000,000 |
Steel | Framing, supports, rebar | 2,000,000,000 |
Wood | Frames, interior finishes | 3,500,000,000 (cubic meters) |
Bricks/Blocks | Walls, partitions | 1,500,000,000 |
It’s dizzying how much the world leans on these few materials, but that’s only the beginning. Specialty additives, chemicals, metals, and synthetics make up the rest, creating buildings that withstand earthquakes, fire, or decades of hard use.
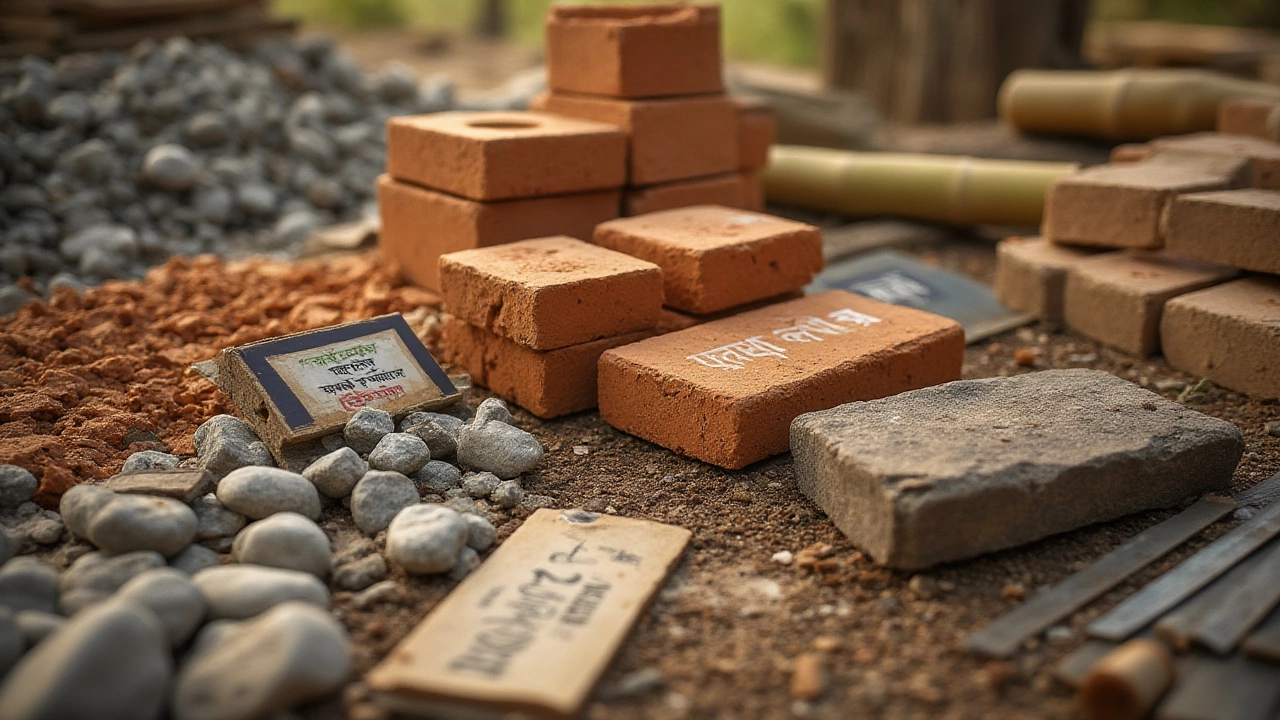
Sourcing, Sustainability, and Impact of Building Materials
Popping into a hardware store makes it seem like these products just appear, but the story starts way before they hit shelves. Most raw materials for construction are ripped from the Earth: mines, forests, quarries—the works. Mining iron ore for steel, scooping up gigantic quantities of gravel and sand for concrete, clearcutting forests for timber—each step leaves a footprint.
Take sand. Not all sand is the same—a special round, tough variety is needed for construction. Yet we’re mining sand so fast that some riverbeds are disappearing, creating fierce turf wars in countries like India. Nobody expected the world to have “sand mafias,” but here we are. The price can skyrocket when supply dips or regulations stiffen.
Lumber’s another hot topic. Construction-grade timber isn’t just any tree chopped down. Trees are selected for straightness, size, species, and then carefully kiln-dried to kill pests. There’s a push for sustainable, certified lumber—think of labels like FSC (Forest Stewardship Council) as the “organic” sticker for wood products. Still, illegal logging remains a billion-dollar problem worldwide.
Steel manufacturing is a huge energy hog. The blast furnaces that create the world’s steel alone account for 7-9% of all carbon emissions globally. Today, a growing chunk of steel comes from recycling old cars or buildings, saving energy and cutting pollution by nearly 60% per ton. The industry trend is clear: if it can be recycled—do it.
Concrete has its own environmental baggage. Cement production (the ‘glue’ in concrete) sends more CO₂ into the air than any country except China and the US. Engineers are now using new recipes, adding materials like fly ash (a power plant byproduct) or slag, to shrink the carbon footprint. It’s not perfect, but every tweak counts. Smart designers look for “green” concrete blends that use fewer resources or last longer, which can add points for LEED certification—a badge of honor for green buildings.
Glass is surprisingly energy-intensive, too. Melting sand, soda, and lime to make large strong panes guzzles power. However, the latest “smart” glass can reduce buildings’ need for heating or air conditioning by automatically tinting or reflecting heat, helping cut total energy use in cities.
Here’s a table showing how sourcing affects the footprint of popular construction materials:
Material | Main Environmental Impact | Key Sustainability Strategy |
---|---|---|
Timber/Wood | Deforestation, habitat loss | Certified sustainable forests, replanting |
Steel | High CO₂ from smelting | Use recycled content, electric furnaces |
Concrete | CO₂ from cement, sand mining | Supplement with fly ash, recycled aggregates |
Glass | Energy for melting, mining | Energy-efficient glazing, recycling cullet |
One tip for a greener build: ask your contractor what percentage of recycled, reclaimed, or certified materials they use. Even a 10% increase can make a huge difference, especially in big projects. Look for local material suppliers—that slashes transport emissions and usually shrinks both your costs and your carbon footprint. If you see buzzwords like "recyclable," "reusable," or "non-toxic," you’re on the right track for tomorrow’s standards.
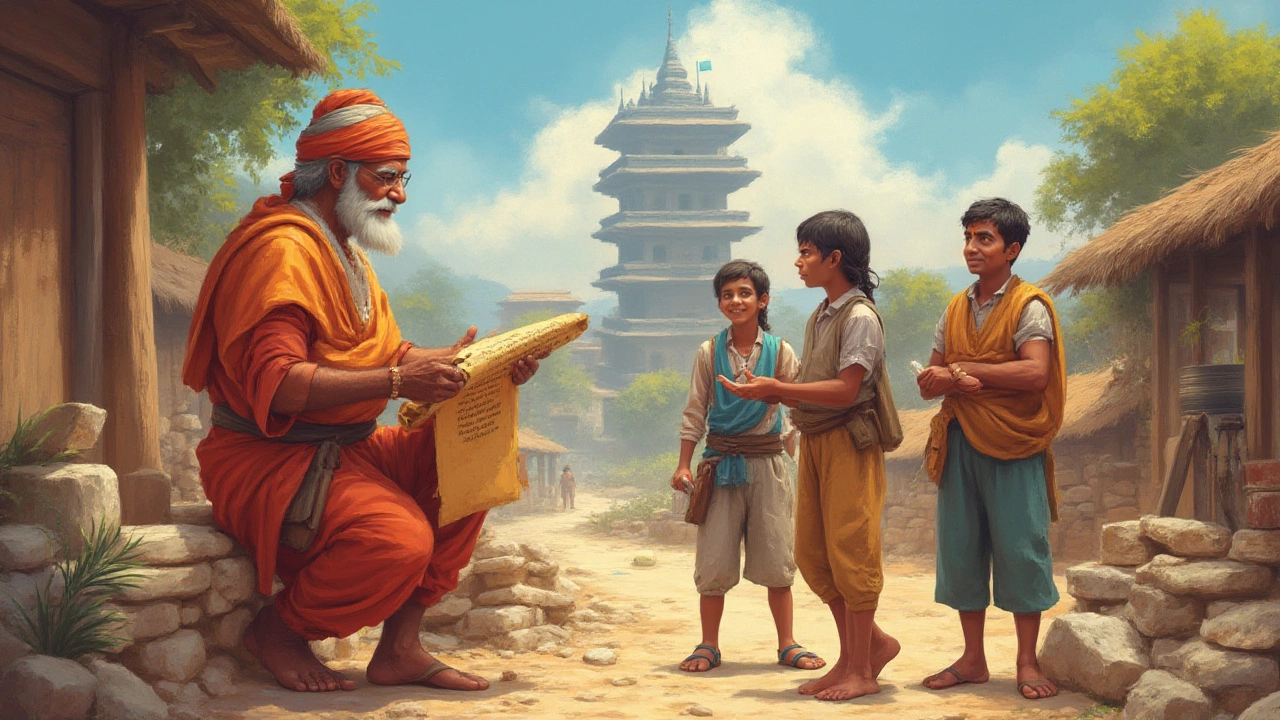
Practical Tips and Trends Shaping the Future of Construction Materials
Staring at endless rows of supplies in a warehouse can be overwhelming. Go past labels and prices—real quality often hides in small details. Here are some hands-on tips to get the most out of your building materials, whether you’re a DIY weekend warrior or on your fourth office complex.
- Know the grade: Construction materials follow grades or specs—think concrete mixes rated by compressive strength or wood sorted by knot patterns. Matching the grade to the job’s needs protects you from early failures and warranty nightmares.
- Moisture matters: Timber with high moisture content (often called “green”) will shrink, warp, or crack after installation. Always check kiln-dried specs for framing or paneling—don’t skimp here.
- Steel secrets: Not all steel is rust-proof. Galvanized or stainless versions work best outdoors or anywhere with leaks or condensation. Skimp here, and you’ll face costly repairs in just a few rainy seasons.
- Mix to match: Concrete isn’t one-size-fits-all. Use high-strength mixes for driveways or heavy loads, lightweight mixes for upper floors, and special fiber-reinforced blends for thin countertops.
- Shop local: Sourcing materials from nearby suppliers not only helps local business, but often results in better-matched materials for your climate, with less risk of warping or damage in transport.
Future trends are re-shuffling the deck for construction materials:
- Engineered wood products—think massive glued-laminated beams or cross-laminated timber (CLT). They’re as strong as concrete, but lighter and made from fast-growing trees.
- Smart materials—self-healing concrete can repair its own cracks by growing tiny crystals inside. Imagine a bridge that fixes itself after freeze-thaw cycles.
- Recycled and alternative plastics—think insulation made from old water bottles, or composite deck boards from recycled bags.
- Transparent aluminum and advanced glass—strong as steel, see-through like glass, these are set to change skylines and unleash wild new design ideas.
- Bio-based bricks—made with bacteria or mushrooms, offering lower carbon impact and new possibilities for insulation and design.
One more tip: regulations around construction materials are getting stricter every year. Fire resistance, earthquake codes, and energy efficiency are driving architects and builders to use smarter, safer materials. Always double-check that what you’re getting is up to code for your area—and don’t trust a verbal guarantee, ask for certifications.
Here’s the bottom line: every piece of a building, from pipes to roof tiles, depends on the marriage of smart engineering and just the right raw material. The right choice means a home that lasts a lifetime, a skyscraper that sways but never shatters, and a blueprint that actually has a future. Next time you gaze at a city skyline, know the real heroes are hidden in every beam, block, and pane—dug, mined, or grown, and engineered for the long haul. The world’s built on more than design. It runs on raw materials, as humble and stubbornly powerful as can be.
Comments