Commercial Construction Methods: What's Involved?
Diving into commercial construction can feel overwhelming with all the options out there. But, don’t sweat it! The basics often start with understanding the key methods used to get buildings off the paper and into the real world. Whether it's shaping a new office space, a retail store, or a whole shopping complex, knowing these methods can make all the difference in achieving both efficiency and quality.
First up, there's traditional construction — the old hand of the commercial building world. It’s the usual suspect, involving tried-and-true practices like on-site fabrication, heavy machinery work, and sometimes, let's just say, a more creative approach to deadlines. This method suits projects that demand detailed customization but can be time-consuming and costly.
- Traditional Construction Methods
- Prefabrication and Modular Building
- Lean Construction Techniques
- Sustainable Construction Practices
- Technology in Construction
- Choosing the Right Method
Traditional Construction Methods
When it comes to commercial construction, traditional methods are still very much in the game. These techniques have stood the test of time, offering a blend of reliability and familiarity that appeals to many builders and architects.
On-Site Construction
One of the hallmarks of traditional building is on-site construction. This means bringing all materials, labor, and equipment right where the action is. It’s like setting up a temporary factory at the job site. Think about big cranes and a lot of construction workers — it’s a hive of activity!
This method allows for a high degree of customization. You want intricate architectural details or complex layouts? This is your go-to option. However, it’s a bit slow and can be affected by weather conditions. Imagine trying to lay bricks in pouring rain; yep, that's a challenge.
Craftsmanship and Material Choices
The beauty of traditional methods is in the craftsmanship. Skilled workers bring a level of detail that machines can't match. Concrete, steel, and brick are standard materials here, each selected based on the project's demands. For example, steel frames are fantastic for skyscrapers due to their strength and flexibility.
The Timeline and Cost Factor
Costs can stack up quickly with traditional construction. Labor-intensive processes, the need for specialized workers, and longer timelines contribute to this. But, if your project has the budget and time, the results can be stunningly detailed and personalized.
Despite newer methods emerging, traditional construction remains relevant. Many still prefer the human touch and aesthetic possibilities it offers. Plus, for certain projects, especially those requiring specific adherence to design, it’s simply the best choice.
Pros | Cons |
---|---|
Customizable design | Time-consuming |
High-quality craftsmanship | Weather-dependent delays |
High material variety | Higher cost |
Prefabrication and Modular Building
Here's the lowdown on prefabrication and modular building, a combo transforming the commercial construction game. Imagine piecing together massive building blocks, only they're not toys but meticulously designed rooms and components. This method takes a chunk of the work off the construction site, bringing it into a controlled factory environment.
Why is that a big deal? Well, it means speed. Modular building can slash construction times by up to 50%, not to mention the cost savings. You're dodging the weather delays and minimizing on-site headaches, a definite win.
How It Works
The process kicks off with design. Components are fabricated in pieces within a factory setup, adhering to strict quality standards. Once they’re ready, these modules are transported to the site where they're swiftly assembled like a giant jigsaw puzzle. This isn't just about walls and roofs; we're talking fully equipped, ready-to-go rooms.
Benefits of Prefabrication
- Cost Efficiency: The overall price tag often dips since there's less waste and a smoother, more predictable workflow.
- Environmental Impact: With less waste and controlled environments, prefabrication tends to be greener and more sustainable.
- Flexibility and Customization: Don't be fooled by the 'factory' setup; there's plenty of room for customization, adapting modules to suit project specifics.
Case Studies & Stats
Like to see some figures? A McGraw-Hill construction report found that nearly 70% of architects use prefabrication and modular methods due to the efficiency and flexibility they offer. And stats show an increasing trend, with numbers jumping 6% from the previous year.
Who’s Already On Board?
Big industry players are hardly strangers to these methods. In healthcare, for instance, constructing hospital wings with prefabricated modules has become increasingly common, cutting the time patients wait for new facilities.
So, thinking about going down this road? Weigh the benefits against your project's specific needs, and you might just find that prefabrication and modular building offer a solid path in commercial construction.
Lean Construction Techniques
If you’ve ever wanted to ditch the fluff and focus on pure efficiency, lean construction techniques might be your jam. Inspired by the lean manufacturing process seen in the auto industry, this approach streamlines operations to minimize waste and maximize value. It's all about getting the job done smarter, not harder.
Principles of Lean
Lean construction focuses on five main principles: identifying value, mapping the value stream, creating continuous workflow, establishing pull processes, and pursuing perfection. By keeping these core ideas in mind, construction projects can often cut down lots of unnecessary or redundant work.
"Lean construction is about doing more with less: less effort, less equipment, less time." - Martin Fischer, Center for Integrated Facility Engineering
One of the coolest things about lean techniques? The emphasis on collaboration. Everyone involved talks, shares insights, and works as a team, kind of like those group projects in school that went shockingly well.
Practical Lean Strategies
So, how do these principles play out in real-world construction? Here's what a lean construction site might focus on:
- Just-in-Time Delivery: Materials arrive when needed, slashing storage costs and reducing clutter.
- Integrated Project Delivery (IPD): Stakeholders across the board—from architects to construction managers—work together from day one.
- 5S Methodology: A tidy workspace isn’t just nice to look at. It also boosts productivity, thanks to the 5S: Sort, Set in order, Shine, Standardize, Sustain.
When to Use Lean Construction
Lean construction techniques tend to be the hero for projects with tight budgets and timelines. It's a game-changer for businesses looking to cut costs without compromising on quality.
According to a report from 2023, construction firms using lean strategies experience an average 20% improvement in productivity.
Year | Productivity Improvement |
---|---|
2021 | 15% |
2022 | 18% |
2023 | 20% |
Is this the future of commercial construction? Could be. With businesses always on the hunt for efficiency, lean construction might just be the toolbox essential to survive the hustle.
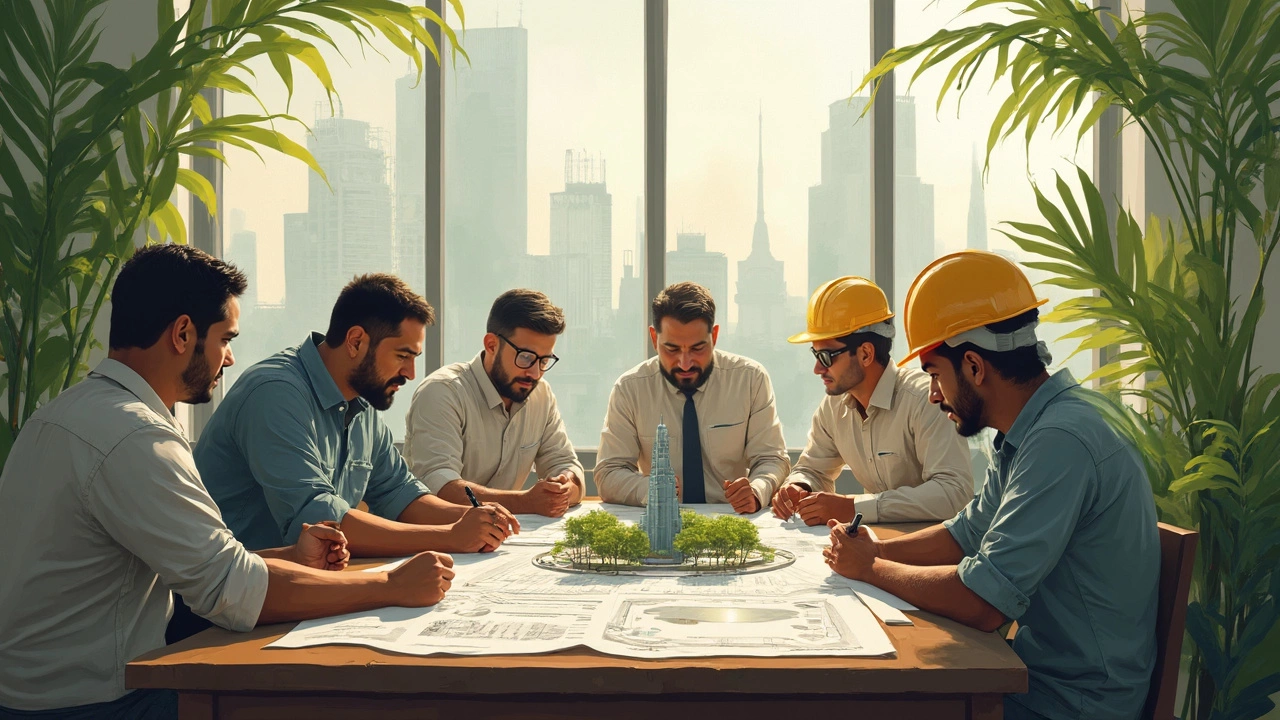
Sustainable Construction Practices
Our planet needs some TLC, and that's where sustainable construction steps in. It's all about reducing the negative footprint that building projects often leave behind. Using materials wisely, cutting down on waste, and ensuring energy efficiency are just a few ways this practice makes a positive impact. It's not just a trend; it’s becoming a necessity as environmental concerns continue to rise.
Consider this quote from the Green Building Council:
“Sustainable construction is not only about building eco-friendly environments; it’s about creating a balance between economic growth and the preservation of the earth.”
Eco-Friendly Materials
One major aspect of sustainable construction is using materials that are kinder to the planet. Things like recycled steel, bamboo, and reclaimed wood are becoming popular choices. These materials not only minimize waste but also often last longer and perform better.
Efficient Energy Use
Another biggie is improving energy efficiency. By incorporating smart designs and modern technologies, buildings can slash their energy consumption. Things like solar panels, LED lighting, and high-efficiency HVAC systems work wonders toward this goal.
Waste Reduction
Waste not, want not! Sustainable construction aims to cut down waste with precise project planning and material selection. Every scrap can have a purpose. Builders are finding creative ways to repurpose materials and reduce landfill deposits.
Water Conservation
Saving every drop is key. Integrating systems like rainwater harvesting and greywater recycling, along with low-flow fixtures, can significantly curb water use in commercial buildings.
Green Certifications
For those looking to prove their green credentials, certifications like LEED (Leadership in Energy and Environmental Design) can be the badge of honor. These standards help ensure that a building meets rigorous environmental performance benchmarks.
Here's a snapshot of how sustainable practices impact construction costs and savings:
Practice | Initial Cost Increase | Long-Term Savings |
---|---|---|
Solar Panels | High | Significant on energy bills |
LED Lighting | Medium | Moderate on energy bills |
Recycled Materials | Low to Medium | Depends on local availability |
Incorporating sustainable methods isn’t just beneficial to the environment. It can also lead to cost savings over time and make properties more attractive to eco-conscious tenants. So, when thinking about your next commercial construction project, going green might just be the smartest move yet!
Technology in Construction
Welcome to the future of commercial construction, where technology isn't just an add-on but a game-changer. It's transforming how buildings are designed, constructed, and even maintained. From drones zipping through the air to AI keeping tabs on project progress, the possibilities are nearly endless.
BIM: Building Information Modeling
One of the shining stars of modern construction is Building Information Modeling (BIM). This is not just a fancy 3D model; it's a digital representation that includes every detail, from the electrical layout to plumbing. BIM helps project managers visualize the project from start to finish, minimizing errors and saving time. It’s like having a digital blueprint that updates itself in real time.
Drones and Robotics
Long gone are the days of guessing what’s happening on-site. Now you can send in drones for a bird’s-eye view to track progress and pinpoint issues. And don't even get me started on robotics; they're handling repetitive tasks, ensuring accuracy, and boosting overall efficiency. Who doesn’t want a robot pal on the construction team?
Virtual Reality and Augmented Reality
Virtual and augmented realities are turning dream projects into tangible plans before a single nail is hammered. They help stakeholders visualize the end project in the planning stage, making adjustments easier and more cost-effective. VR and AR aren’t just cool toys; they’re incredible tools for commercial building projects.
Cloud-based Collaboration Tools
In today’s construction landscape, teams are scattered across different locations, making collaboration a challenge. Enter cloud-based tools. These platforms allow for seamless communication, document sharing, and problem-solving — no matter where team members are located. It's like having a virtual office that everyone can access.
The Data Goldmine
With all this tech, you’re probably knee-deep in data. Fortunately, smart data analytics can sift through it to spot trends, forecast delays, and even predict maintenance needs. Talking about smart management, right? It turns the unpredictability of construction work into a more manageable, efficient process.
The takeaway? Technology in commercial construction isn't just the future; it's the present. Adopting these innovations can cut costs, save time, and lead to a higher quality build. Just consider these technologies your construction toolkit essentials.
Choosing the Right Method
When it comes to commercial construction, picking the right building method is like choosing the right tool for the job. It's crucial to weigh your options based on what the project demands. There’s no one-size-fits-all, and flexibility often makes a big difference.
Consider the Project's Scale and Complexity
The first thing to check is the project’s scale and complexity. Smaller projects, like local offices or retail spaces, may not need the extensive planning that a shopping mall might require. Prefabrication or modular methods might be best for simpler setups, offering speed and cost benefits.
Timeframe and Budget
Your timeline and budget are two sides of the same coin. If you're in a rush, prefabricated options can fast track your project. On the flip side, if budget is your main concern, traditional methods with local materials can sometimes offer savings. But remember, cheaper isn't always better if it leads to compromises on quality.
Environmental Impact
Going green isn’t just a trend. More businesses are considering sustainable construction practices that lessen environmental impact. These methods might include using eco-friendly materials or building energy-efficient structures. The upfront costs might be higher, but they often pay off down the line.
Workforce Availability
Don't forget about the workforce. Some construction techniques require specialized skills. Check the availability of skilled labor in your area, especially if you’re considering advanced methods like modular building or cutting-edge tech-based approaches.
Tech Integration
Technology plays a huge role now. From 3D modeling to BIM (Building Information Modeling), integrating modern tools can smooth out wrinkles in planning and execution. Tech can also improve precision, saving time and money in the process.
Ultimately, finding the best method involves balancing these factors with your project goals. Talk to experts, do the research, and make choices that align with your long-term vision. By taking a well-rounded approach, you'll save yourself a lot of potential headaches and setbacks.
Comments